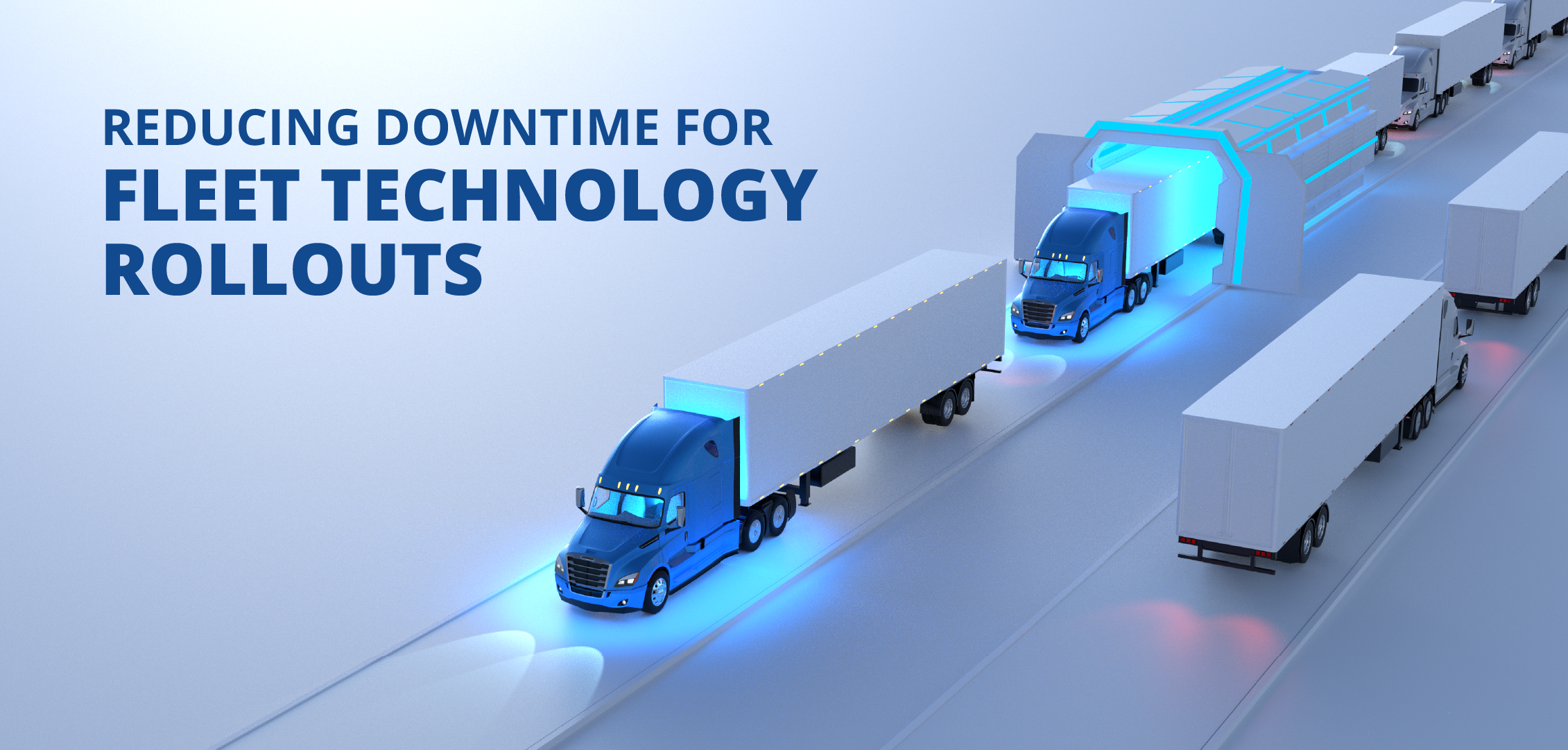
Reducing Downtime for Fleet Technology Rollouts
Even with new technologies, systems, and equipment for improving operations and efficiencies—some of which may be required by law—the idea of systematic change is often dreaded by large fleet managers. Many have learned from experience that downtime means lost revenue and momentum. However, with proper planning and strategic partnerships, you can deploy new fleet technologies as painlessly as possible while saving time every day.
The Benefits of Upgrading Your Fleet’s Technology
By now, all large-scale American and Canadian fleets are familiar with electronic logging devices (ELDs) and their legal requirements. When the implementation of ELD mandates began nearly a decade ago, fleets continued—or completed—their transition from paper logs to electronic devices. Motivated by a need for more accurate and consistent reporting, ELDs were envisioned as helping reduce hours of service (HOS) violations and end-of-haul paperwork, and creating safer roadways for both commercial motor vehicles (CMVs) and passenger vehicles.
As fleet management technology evolved, unexpected benefits began to emerge. Fleet managers could access vast amounts of data related to their operations, including real-time information related to vehicle statuses, maintenance, routes, and gaps in driver training. Today’s leading ELD providers now offer tools for improving the driving experience, such as electronic driver vehicle inspection reports (eDVIRs), truck-based navigation, and circle of service data. The potential for ELDs is virtually limitless and enables fleet managers to dive as deep as they want into understanding the health of their fleets. The key is finding fleet management technologies that are flexible enough to fit—and grow with—your operations and easily deploy to your entire fleet quickly and efficiently.
Seven Ways to Optimize a Fleetwide Rollout
1. Ask the Right Questions
In addition to being a major financial investment, a new fleet management platform represents a long-term relationship with your vendor. To avoid negative surprises down the road, it’s important to do your research, get buy-in and input from team members across your operations, and ask potential vendors as many questions as possible. Take time to do your homework on any new hardware you’ll be using, and be sure to check reviews and peer experiences. (For more tips and ideas, download the free guide, 6 Secrets of Fleet Management Software Buyers)
2. Keep an Eye to the Future
Make sure the platform you choose is customizable and built to grow with your operations. Hardware and software elements should be future-proofed, scalable, and capable of evolving as your needs change over time. This saves you downtime in the future when new needs evolve or new technologies become available. Be sure to choose a vendor who is active and involved in the industry with a good track record of thought leadership. Once you’ve found the right match, set expectations about how they’ll support your company as it grows and as the industry evolves.
3. Look for Seamless Integrations
Ensure your new fleet management tools integrate seamlessly with your transportation management system (TMS). Ask vendors about their integration processes, timelines, and user experience processes for drivers and back-office teams. Choose a vendor with strong technology partnerships who can ensure smooth handshakes with the other apps and tools your drivers need on a daily basis. Additional benefits include products that consolidate drivers’ most-used apps into a centralized control center or streamlined functionality to improve ease-of-use and safety.
4. Set Realistic Timelines and Goal Markers
Communication is key in planning your rollout. Make sure your vendor is aware of your operations and truck availability. A good partner will provide a dedicated account representative who is familiar with your fleet’s schedules and goals. Work to create a timeline—including training and other needed support—and establish smaller “sprints” that ensure you’re on track with your overall timeline. Catching a smaller missed deadline makes it easier to correct your course along the way.
5. Get Driver Feedback Often
Be sure to keep lines of communication open, especially with those most frequently using your new tools. Check in with them to see what works and what doesn’t, as well as any areas requiring additional training or guidance. Consider a ride-along to see how the product works in real time and to learn how to clearly communicate any feedback to the vendor. After you’ve provided feedback, make sure to close the loop on any questions or concerns to confirm all issues are resolved.
6. Take Advantage of Transportation Safety Planning (TSP) Tools
Dig into your route data and driver performance to get a comprehensive picture of your operations’ strengths and potential areas for improvement. In addition to providing electronic logging device (ELD) data, transportation safety planning (TSP) tools enable you to monitor vehicle performance and maintenance, hard breaks or turns, dashcam footage, and more. These data points help you identify gaps in operations and set benchmark metrics to guarantee improvements over time.
7. Consider Going the Pre-Installed Route
With fleet management tools continuing to advance, leading software providers are partnering with truck manufacturers and OEMs to produce vehicles with pre-installed devices for managing fleet data. For example, Platform Science’s partnerships with Daimler Truck North America, Navistar, and PACCAR enable fleets to use factory-installed hardware, reducing the total cost of ownership, eliminating the need for aftermarket installations, and reducing overall downtime.
Putting the work in ahead of your rollout helps remove any roadblocks and preventable issues that could potentially slow down the transition to your new system. With the help of an experienced partner and staff buy-in—from leadership and drivers to your back-office team—you’ll see that teamwork and a shared vision make even the largest rollout go smoothly. When your data starts flowing in, you’ll be able to identify positive operational changes that make everyone’s job easier, an investment that pays off for years to come.
At Platform Science, we’ve helped hundreds of fleets plan and efficiently implement their system upgrades. We’d love to help you roll out your fleet’s new technology, too, so connect with us to learn more.
